Concrete Installation: The Complete 7-Step Process
Three crucial steps set the stage for success in the preparation phase of any project: site inspection and analysis, gathering necessary permits and permissions, and clearing and leveling the area.
Site Inspection and Analysis
Conducting a thorough site inspection and analysis is essential before starting any construction or development work. This involves assessing the land's terrain, soil composition, and existing structures or obstacles. Project managers can identify potential challenges and opportunities by carefully examining the site, allowing for better planning and resource allocation.
Gathering Necessary Permits and Permissions
This process involves submitting applications to relevant authorities and securing approval for the proposed project. The project's nature and location may require permits for construction, environmental impact, zoning, and more. Please ensure the necessary permits to avoid costly delays and legal complications.
Clearing and Leveling the Area
Once all necessary approvals are in place, the next step is to clear and level the construction site. This typically involves removing any vegetation, debris, or existing structures that may interfere with the project. Additionally, the land may need to be graded or leveled to create a stable foundation for construction. Proper si e preparation ensures that construction can proceed safely and efficiently.
By prioritizing these preparatory steps, project teams can lay the groundwork for successful execution. Thorough preparation is critical to minimizing risks and maximizing outcomes, from assessing the site's suitability to obtaining legal clearance and preparing the land.
During the formwork setup phase of a construction project, several critical tasks are essential to ensure the proper shaping and reinforcement of concrete structures.
Building the Forms to Shape the Concrete
The first step in formwork setup is constructing the forms that will shape the concrete. These forms act as molds, guiding the concrete into the desired shape during pouring and curing.
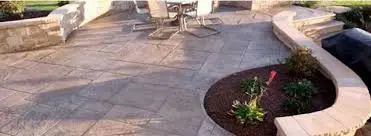
Ensuring Prop Alignment and Stability
Once the forms are in place, it's crucial to ensure they are correctly aligned and stable. Misaligned or unstable forms can result in irregular concrete shapes and compromised structural integrity. Workers carefully check and adjust the forms to ensure they are level, plumb, and securely anchored to the ground or existing structures.
Adding Reinforcement if Required
In some cases, additional reinforcement may be needed within the forms to strengthen the concrete structure. This reinforcement, often in steel bars or mesh, is added before the concrete is poured to provide extra support and prevent cracking or failure under load. Engineers assess the structural requirements and specify the type and placement of reinforcement accordingly.
By diligently following these steps, construction teams can ensure the successful setup of formwork for concrete structures. Properly built forms, aligned for stability and reinforced as necessary, lay the foundation for a durable and reliable construction project.
These are the essential steps that need to be followed:
Selecting the Right Concrete Mix
Choosing the appropriate concrete mix is crucial for the success of any construction project. Factors such as the intended use of the concrete, environmental conditions, and project specifications influence the selection process. Different mixes are available, each with unique properties like strength, durability, and workability. Contractors work closely with engineers to determine the optimal mix for the job.
Mixing the Concrete to Proper Consistency
Once the concrete mix is selected, it's time to prepare it to ensure proper consistency. This involves combining cement, aggregates (such as sand and gravel), water, and sometimes additives or admixtures. The mixture is blended thoroughly to ensure uniformity and achieve the desired workability. Consistency ensures concrete can be easily placed, compacted, and finished on-site.
Testing for Quality and Uni enormity:
Before pouring, the concrete undergoes rigorous testing to ensure its quality and uniformity. Samples are taken and subjected to various tests, including slump tests to assess workability, compressive strength tests to measure load-bearing capacity, and air content tests to detect entrapped air. These tests help identify any issues with the concrete mixture and allow adjustments to be made as needed to meet project specifications.
By carefully selecting the right concrete mix, ensuring proper consistency during mixing, and conducting thorough quality testing, construction teams can ensure that the concrete used in their projects meets the highest quality and performance standards. This attention to detail is essential for the durability and longevity of structures, whether they're simple sidewalks or complex high-rise buildings.
During the pouring and placement phase of a construction project, careful attention to detail is essential to ensure the proper installation of concrete. Here's how this process unfolds:
Pouring concrete is not just about dumping it into the forms; it requires a strategic approach. Workers carefully pour the concrete into the forms in a controlled manner, ensuring even distribution and avoiding segregation. This process typically uses concrete pumps or chutes to reach difficult-to-access areas.
Spreading and Leveling the Concrete:
Once the concrete is in place, it must be spread and leveled to achieve the desired surface finish. Workers use tools like screeds, floats, and trowels to distribute the concrete and create an evenly smooth surface. Proper leveling is crucial for ensuring structural integrity and aesthetics.
Consolidating and Removing Air Pockets
Consolidating the concrete involves compacting it to remove trapped air pockets and ensure maximum density. Removing air pockets is essential for preventing weaknesses and achieving uniform strength throughout the concrete structure.
Whether it's a foundation, slab, or structural element, proper pouring and placement techniques are essential for achieving quality results that meet project specifications and withstand the test of time.
The curing and protection phase is critical for ensuring the strength, durability, and longevity of concrete structures. Here's how it's done:
Covering the Concrete to Retain Moisture:
Immediately after placement, concrete must be covered to retain Moisture, which is crucial for proper curing. Covering methods include using wet burlap, plastic sheets, or curing blankets to keep the concrete moist during the curing process.
Applying Curing Compounds or Sealers:
In addition to moisture retention, curing compounds or sealers may be applied to the concrete surface to enhance curing. These compounds form a protective barrier that helps to retain Moisture and prevent the evaporation of water from the concrete. Curing compounds also achieve a more uniform process, producing more robust and durable concrete.
Protecting the Concrete from External Factors:
During the curing period, protecting the concrete from external factors that can negatively impact its strength and appearance is essential. This includes protecting it from harsh weather conditions such as extreme heat, cold, or rain, as well as from traffic or other physical damage. Proper protection ensures the concrete can cure undisturbed and achieve its intended properties.
Construction companies can ensure the proper curing and protection of concrete structures by covering them to retain Moisture, applying curing compounds or sealers, and protecting them from external factors. This attention to detail during the curing process is essential for maximizing the concrete's strength, durability, and longevity, ultimately resulting in high-quality finished projects that meet or exceed expectations.
In the finishing phase of a concrete project, attention shifts to refining the surface appearance and functionality. Here's how it's accomplished:
Joints and control lines are strategically placed in the concrete to control cracking and provide structural integrity. Properly placed joints help prevent unsightly cracks and ensure the long-term durability of the concrete.
Addin Decorative Elements if Desired:
Decorative elements can be added during the finishing phase for projects requiring more aesthetic appeal. This may include staining or coloring the concrete, embedding decorative aggregates or patterns, or applying coat ngs for added protection and visual appeal. Decorative elements allow for customization and creativity, enhancing the overall look and feel of the finished project.
By focusing on smoothing and texturing the surface, creating joints and control lines, and adding decorative elements if desired, construction teams can achieve a polished and professional finish for their concrete projects. Whether it's a simple sidewalk, driveway, or intricate decorative concrete feature, attention to detail during the finishing phase ensures a high-quality result that meets functional and aesthetic requirements.
During the final inspection, thorough checks are conducted to identify any cracks, defects, or imperfections in the concrete surface. This includes visually inspecting the entire structure and using specialized tools to detect hidden flaws. Identifying these issues early allows for timely intervention and prevents potential problems from worsening.
If any cracks, defects, or imperfections are found during the inspection, prompt action is taken to address them. This may involve filling cracks, patching holes, or applying coatings to protect the surface. Repairing these issues ensures the structural integrity and appearance of the concrete, prolonging its lifespan and preventing further damage.
Once the inspection and repairs are complete, guidance is provided on adequately maintaining and caring for the concrete structure. This includes recommendations for routine maintenance tasks such as cleaning, sealing, and resealing to protect the surface from environmental factors and wear and tear. Proper maintenance helps preserve the integrity and appearance of the concrete over time, reducing the need for complete repairs or replacements.
By conducting a thorough final inspection, making necessary repairs or corrections, and providing guidance on maintenance and care, construction teams can ensure that the concrete structure meets or exceeds quality standards and remains in optimal condition for years.
FAQs
1. Why is final inspection necessary for concrete projects?
Final inspection ensures the concrete structure is free from defects or imperfections, ensuring its long-term durability and performance.
2. What are common defects found during the final inspection of concrete projects?
Common defects include cracks, spalling, scaling, and surface imperfections.
3. How often should concrete structures be inspected for maintenance purposes?
Regular inspections are recommended to identify and address emerging issues before they worsen. Inspections may be conducted annually or semi-annually, depending on the usage and environmental conditions.
Conclusion:
In conclusion, completing a concrete project requires careful attention to detail at every stage, from preparation to final inspection and maintenance. By following best practices, conducting thorough inspections, and addressing any issues promptly, construction companies can deliver concrete projects that meet or exceed expectations.
Are you planning a concrete project? Ensure its success by partnering with us as we are experienced professionals who understand the importance of proper preparation, execution, and maintenance. Let's build something great together!
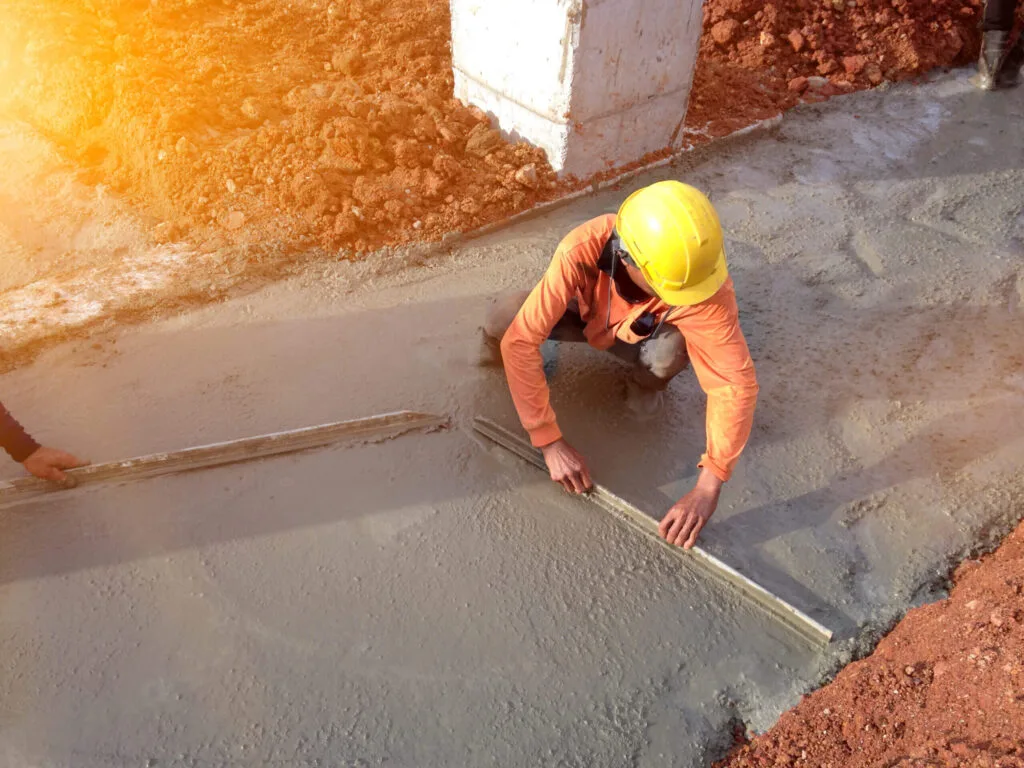